|
|
|
|
|
|
|
|
|
|
|
|
|
|
|
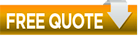 |
|
|
|
SERVICES
|
|
|
|
|
|
|
|
|
|
|
|
|
|
|
|
|
MW
Installers is dedicated to delivering customer satisfaction by
following proper installation techniques & procedures required by
law to transport your mobile home.
Mobile Home & Modular Installation Services include:
- Florida State Licensed Mobile home Mover & Installer
(Florida State License # IH-1025198)
- Re-leveling all size Mobile homes - Retro fit your existing Mobile home To Meet State Regulating
Standards Of Code 15C-1 - Replacing old Mobile Home rusted anchors with new galvanized
anchors - Proper Spacing - Add additional foundation piers
MW modular Installers & Mobile Home Movers procedures and
installation services act in accordance with standards set by the
Department of Highway Safety and Motor Vehicles for the proper
installation and setting of mobile/manufactured homes and park
trailers. For More Information on Florida Code 15C-1 Please Read The Section
Below.
Florida Administrative Code 15C-1
It's not just hurricanes that require special attention by owners of
manufactured homes in Florida. Many manufactured home owners in
Florida create an assumption that hurricanes are the only natural
weather phenomenon that their manufactured home needs protection
from. Along with the correlated risk associated with living in
Florida and hurricanes also comes a very high risk of experiencing
violent thunderstorms in summer months, with lightening, strong
winds and tornadoes, owners of manufactured homes need to keep all
weather conditions in mind when planning to protect their home and
make sure that installation of their manufactured/mobile home is
performed in accordance with Florida Administrative Code 15C-1.
Prior to the vast amounts of devastation and damage to
manufactured/mobile homes caused by the winds of Hurricane Andrew in
1992, the pier and anchor placement was determined by local county
codes. Shortly after hurricane Andrew the Florida Department of
Motor Vehicle (DMV) implemented a very strict state code for all
Manufactured/Mobile Home installation.
15C-1.0102 Installation Standards for Mobile/Manufactured Homes and Park
Trailers.
The standards set forth herein are requirements for all
mobile/manufactured home and park trailer installations, unless
otherwise specified in this rule. All installations of
mobile/manufactured homes shall be performed by either a licensed
installer, dealer installer or manufacturer installer.
Easy Directory Links:
1.
Installation Standards 2.
Anchors, Piers And Tie-Down Components 3.
Site Preparation 4.
Auger Anchors 5.
Stabilizing Devices 6.
Foundations, Piers, And Load Bearing Support Devices
Installation standards
Installation standards for the set-up of new or used manufactured
homes and park trailers shall be in compliance with the manufacturer
installation instructions unless otherwise specified in this rule.
In the absence of the manufacturer installation instructions, used
mobile/manufactured homes and park trailers shall comply with the
provisions of this rule. The park trailer manufacturer shall make
built-in provisions for a minimum of three (3) vertical tie-down
straps and three (3) frame tie-down straps on each side of the unit.
All used park trailers shall have at least three (3) vertical and
three (3) frame tie-down straps installed. Exception: The center
vertical tie-down strap on used units may be exempt when it is
structurally prohibitive to install.
Anchors,
Piers and Tie-Down Components
All anchors, piers and tie-down components used in the installation
of a mobile/manufactured home or park trailer shall be tested,
listed and approved by the Florida Department of Highway Safety and
Motor Vehicles, Bureau of Mobile Home and Recreational Vehicle
Construction. If tests are conducted out of the State of Florida,
the anchor or component manufacturer shall pay the expenses (per
diem and travel) incurred by this out-of-state travel. Installation
of such anchors, piers and tie-down components shall be in
accordance with the manufacturer instructions used during the
testing procedure.
Site Preparation
Site Preparation: The under-home grade (ground) shall be cleaned of
all vegetation and organic material; i.e., stumps, roots, etc.,
except grass not exceeding three inches (3'') in height. The area
beneath and around the home shall be graded, sloped for proper
drainage so that water will not accumulate under the home. All grass
and organic material shall be removed and the pier foundation placed
on stable soil or compacted fill. When the soil compaction or soil
bearing capacity is not known, assume one thousand (1,000) psf or
consult with the local building authority. Soil shall be removed
from an area of at least 16'' 16'' to a depth equal to the height of
the pier base. Exception: When being installed on fresh, clean,
compacted fill the pier base may be placed on top of the soil. The
bottom of the footer(s) shall be placed on stable soil. The pier
foundation shall be a minimum of 4'' 16'' 16'' solid concrete pad,
pre-cast or poured eight inch (8'') minimum in place, or other
material approved and listed by the department. Where the
manufacturer specifications have additional requirements than the
above, the more stringent shall apply.
Auger Anchors
Auger Anchors: All mobile/manufactured homes and park trailers shall
be anchored with approved auger anchors, which shall be coated with
hot-dipped zinc galvanizing (ASTM Standard #123-89A, which is hereby
incorporated by reference); .60 ounces per square foot. Auger
anchors shall be installed to the manufacturers installation
instructions with special emphasis on soil classification and placed
in undisturbed or compacted soil. Piers are to be installed off
center of the anchors so as not to interfere with the proper
alignment of the strapping. Anchors may be installed in predrilled
holes provided the anchor penetrates a minimum of two feet (2') into
undisturbed soil beyond the predrilled hole. When the anchor
manufacturer installation instructions permit, the hole is then
backfilled with soil compacted in layers not exceeding six inches
(6''). For manufactured homes produced after July 13, 1994, refer to
the manufacturer set-up manual for the working load requirements for
anchors at the different tie points on the manufactured home. For
used manufactured homes manufactured after July 13, 1994, and the
manufacturer set-up manual is not available, all anchor points at
side walls, shear walls, end walls, center line and other points as
identified by the manufacturer, shall be certified for a working
load of four thousand (4,000) pounds, with an ultimate load of six
thousand (6,000) pounds. Anchors are required one at each end of
shear walls; one on each end of each I-beam; one frame tie at each
vertical tie point; one on each end of each marriage wall (center
line); and on each ridge beam support post. Note: Coral anchors are
not designed to meet Zone II and Zone III wind requirements.
Stabilizing Devices
Stabilizing Devices: All ground anchors shall have approved
stabilizing devices approved by the department, each of which shall
have a minimum surface area of 180 square inches and shall be coated
with hot-dipped zinc galvanizing (ASTM Standard 123-89A, which is
hereby incorporated by reference); .60 ounces per square foot or
zinc coated to ASTM (A929/A 929M-96, which is hereby incorporated by
reference). The stabilizing device shall be installed with the top
of the stabilizing device installed flush with the soil to prevent
the anchor from deflecting. Exception: Stabilizer devices are not
required at center line or marriage wall locations unless required
by the manufacturer set-up manual.
Foundations, piers, and load bearing support devices
Foundations, piers or other load bearing supports or devices shall
be installed and constructed to evenly distribute the load. Steel
piers with mechanical adjustments shall be securely attached to the
frame of all mobile/manufactured homes or park trailers. (See Figure
C in Rule 15C-1.0103, F.A.C.) Manufactured load-bearing supports or
devices shall be listed and approved for the use in which it was
applied or piers shall be constructed as outlined in this rule.
Concrete products shall comply with the following specifications:
Minimum dimensional and structural requirements for load-bearing
solid and cell concrete blocks shall be to the Standard
Specification for Load-Bearing Concrete Masonry Units, ASTM C-90,
1996 edition. Concrete foundations and cap blocks must have a
minimum of two thousand two hundred (2,200) pound flexural strength
as measured by Standard Test Method for Sampling and Testing
Concrete Masonry Units, ASTM C140-96. Solid 4 concrete blocks are
the minimum thickness of blocks that will meet this test. Poured
concrete shall be a minimum of fcl = 2500 PSI. All plastic products
shall be conditioned to ASTM D 618-61, reapproved 1990, Standard
Practice for Conditioning Plastics and Electrical Insulating
Materials for Testing. Plastics shall be tested to the following
standards: ASTM D 790-92, Standard Test Methods for Flexural
Properties of Unreinforced and Reinforced Plastics and Electrical
Insulating Materials; ASTM D 732-85, Standard Test Method for Shear
Strength of Plastics by Punch Tool and ASTM G 53-88, Standard
Practice for Operating Light and Water Exposure Apparatus for
Exposure of Nonmetallic Materials. All of the above ASTM Standards
in subsection (6) are hereby incorporated by reference.
Specific Authority 320.011, 320.8325(2) FS. Law Implemented
320.77(10), 320.822(12), 320.8285, 320.8325, 320.835(2) FS. History
ew 1-10-94, Amended 10-2-95, 3-31-99.
|
|
|
|
|
|
|
|
|
|